Why Is Good Engineering Practice [GEP] Important In The Pharmaceutical Industry?
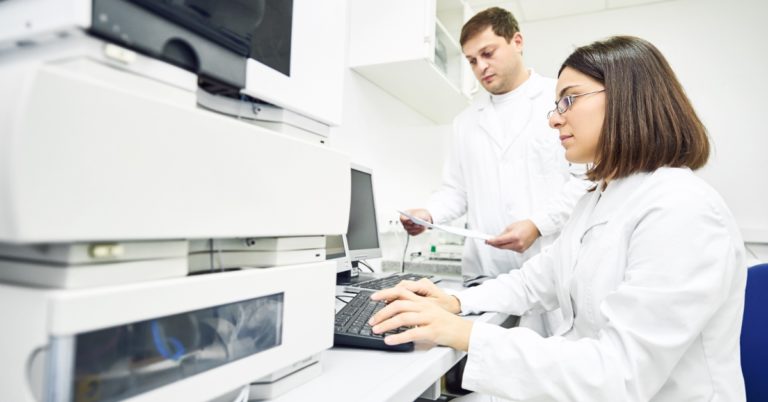
Every industry has some kind of associated risk – some are “lucky” enough to only have to face financial risk, while others face the ultimate risk when it comes to the safety of its consumers (i.e., patients).
Manufacturing pharmaceuticals is most certainly a high-risk industry to be in. However, high risk usually can also mean high reward, which can often times entice drug manufacturers to lose focus on safety and compliance versus profits.
This article discusses establishing an effective Good Engineering Practice (GEP) process that engineering and quality assurance organizations can use to help improve operational excellence and minimize or eliminate potential risks to product quality.
Why Use GEP?
Use of GEP principles improve project outcomes, team productivity, cost efficiencies, process understanding, quality assurance, and also helps to more easily achieve regulatory compliance and implement technological innovation.
What Is GEP?
So, what is GEP? ISPE defines GEP as – “Established engineering methods and standards that are applied throughout the project lifecycle to deliver appropriate and cost-effective solutions.”
What Does The GEP Process Include?
The GEP process should take full account of all applicable project and user requirements, including GxP, safety, health, environmental, ergonomic, operational, maintenance, recognized industry standards, and other statutory requirements.
The GEP process includes:
- Specification
- Design
- Verification Review
- Approval Activities
Is GEP Required?
GEP is not mandated by GMP regulations. However, effective implementation and use of GEP principles improves project outcomes, team productivity, cost efficiencies, and also drives technological innovation and compliance.
Institutionalizing GEP policies and procedures in a controlled EQMS that adequately define how to establish well-defined project and user requirements, and progress monitoring and control strategies is essential for right-the-first-time delivery of critical-to-business projects in compliance with GxP regulatory expectations.
Adequate provisions related to quality and risks should be included in specification, design, procurement, and other contractual documents for engineered systems. Life-cycle documentation covering risk assessments, planning, specification, design, verification, installation, commissioning and qualification, owner turnover acceptance, and maintenance should be produced as part of GEP.
What Are Some Good Engineering Best Practices?
In the pharmaceutical industry, adherence to rigorous engineering best practices is paramount to ensuring product quality, regulatory compliance, and patient safety. Key practices include meticulous documentation of processes, adherence to industry standards, comprehensive validation and testing, robust risk management, and adherence to Good Manufacturing Practice (GMP) guidelines.
Project Infrastructure
Project is so important to pharmaceutical engineering because the industry is so highly regulated. By understanding and creating an infrastructure, it helps facilitate comprehensive documentation, data integrity, and traceability, which are fundamental for regulatory inspections and audits.
Essentially, project infrastructure acts as the backbone, ensuring that pharmaceutical engineering projects are executed efficiently, adhere to regulatory requirements, and produce safe and high-quality pharmaceutical products.
The first component of institutionalizing effective GEP in an organization looking to gain the full benefit of GEP is to have written standards and procedures for the key concepts and elements of GEP.
These policies, standards, procedures should be supported by the same controls for documents and documentation utilized in a manufacturing environment’s Quality Management System.
The QMS establishes the foundation for a highly effective, documented and executed design, specification and verification process. QMS policies and procedures enable the standardization of best practices in an organization leading to engineering ‘operational excellence’.
This will result in consistently delivering and achieving cost-effective engineered solutions that meet critical user-defined requirements and assures that the system is fit for its intended use.
Implementation
The implementation of Good Engineering Practices (GEP) is imperative in pharmaceutical engineering due to the industry’s strict regulatory landscape.
Adhering to GEP principles, including Good Manufacturing Practice (GMP), is essential to meet rigorous standards governing the safety, efficacy, and quality of pharmaceutical products.
GEP establishes a systematic approach to risk mitigation, emphasizing efficient and consistent engineering practices that contribute to streamlined processes and reduced variability.
Ultimately, the rigorous application of GEP principles in pharmaceutical engineering serves as a cornerstone for navigating industry complexities, upholding quality standards, and safeguarding patient well-being by ensuring the delivery of safe and effective pharmaceutical products.
Operation and Maintenance
The three concepts at the core of most GEP activities include:
- Risk Management
- Cost Management
- Organization and Control
The significance of operations and maintenance disciplines lies at the core of ensuring the sustained functionality, efficiency, and reliability of industrial systems and facilities.
Operations focus on the day-to-day activities involved in running these systems, encompassing processes such as production, monitoring, and troubleshooting.
Maintenance, on the other hand, is dedicated to preserving the integrity of equipment and facilities through regular inspections, repairs, and preventive measures. The seamless integration of these disciplines is essential for optimizing overall operational performance.
What Does Your GEP Process Look Like?
GEP serves as a unifying force between operations and maintenance disciplines, promoting shared practices such as meticulous documentation, continuous training, and a commitment to safety.
By following good engineering practices, industrial professionals enhance operational efficiency, mitigate risks, and achieve sustainable success.
Article By: Sam DeMarco