What Is CAPA? Ultimate Guide To FDA Corrective And Preventive Actions
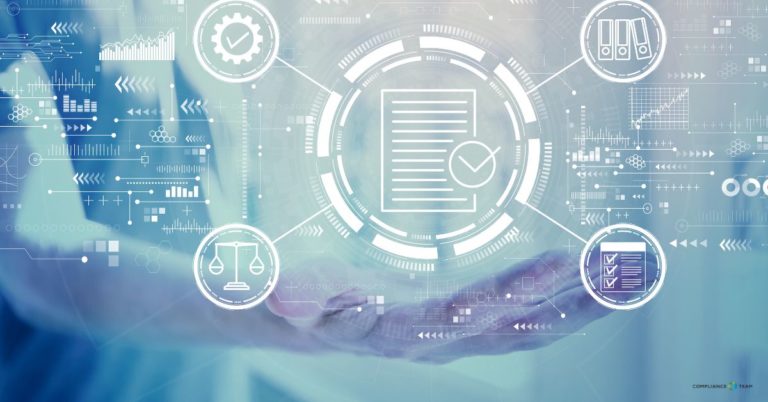
In today’s highly regulated industries, maintaining product quality and safety is paramount. Corrective and Preventive Action (CAPA) is a critical component of any quality management system, ensuring that potential and actual issues are systematically identified, investigated, and addressed.
CAPA processes are not only vital for improving product reliability and customer satisfaction but are also mandated by regulatory bodies such as the FDA. Effective CAPA implementation can prevent recurring problems, mitigate risks, and ensure compliance with stringent regulatory requirements.
This article delves into the essential aspects of CAPA regulatory compliance, exploring its phases, methods, and best practices to help organizations achieve and maintain the highest standards of quality and safety.
What Is CAPA?
CAPA, which stands for corrective and preventive actions, is like a series of mini analysis’s that help identify any potential issues in a process or product. It’s a preventive process that allows those in the industry to identify any risk management issues a little at a time and work on them, rather than being hit with a stream of issues at once.
Why Is CAPA Important?
CAPA is crucial for ensuring product safety, quality, and regulatory compliance. It helps organizations proactively identify and mitigate risks, preventing issues from recurring and ensuring continuous improvement.
CAPA Regulatory Compliance Phases
It’s essential for any company to follow the regulatory compliance phases to not get lost within the process and be able to properly proceed for a successful result. Let’s take a look at the typical phases a CAPA procedure consists of.
Preparation
Preparation is important for the success of any CAPA system. Before a company starts diving in, be sure that you have the appropriate CAPA forms and SOPs before starting. This groundwork commences with the creation of your CAPA procedures document, a comprehensive set of guidelines delineating your organization’s approach to managing CAPA.
The CAPA procedures document outlines the objectives, criteria, steps, and responsibilities integral to the CAPA system. It serves a dual purpose as an internal reference for your team and as formal documentation for regulatory bodies.
Take note that the absence or inadequacy of CAPA procedures stands out as one of the most frequently cited reasons for FDA 483 observations and warning letters. The robustness of your CAPA procedures is central to maintaining compliance and effectively navigating regulatory scrutiny.
Identification
The identification phase in CAPA involves recognizing and documenting potential or actual problems from sources like customer complaints or audits. It includes collecting relevant data, formally reporting the issue, and performing a preliminary risk assessment to prioritize and classify the problem.
The process ensures compliance with regulatory requirements and sets the stage for initiating corrective or preventive actions. Accuracy, traceability, and timeliness are crucial for effective problem identification and subsequent CAPA success.
Investigation
The investigation phase in CAPA involves a thorough analysis of the root cause of the identified problem, using techniques like root cause analysis or failure mode and effects analysis (FMEA). Data is collected, reviewed, and analyzed to understand the underlying issues, and hypotheses are tested to confirm the cause.
The findings are documented comprehensively, ensuring traceability and compliance with regulatory requirements. This phase culminates in defining specific corrective and preventive actions to address the root cause and prevent recurrence.
Implementation
The implementation phase in CAPA involves executing the defined corrective and preventive actions to address the identified root cause of the problem. This includes assigning responsibilities, setting timelines, and ensuring resources are available for effective action.
The actions are carried out, monitored, and documented to verify their completion and effectiveness. Compliance with regulatory requirements is maintained throughout, ensuring the problem is resolved and future occurrences are prevented.
Verification
The verification phase in CAPA ensures that the implemented corrective and preventive actions effectively address the root cause of the problem. It involves monitoring and evaluating the outcomes to confirm that the issue is resolved and does not recur. Documentation of the verification process is crucial for traceability and regulatory compliance. This phase concludes with a final review and approval to confirm the CAPA process’s success and closure.
FAQs On CAPA Regulatory Compliance
Let’s take a look at some of the most commonly asked questions regarding CAPA regulatory compliance.
What methods are used to investigate the root cause in CAPA?
Common methods include Root Cause Analysis (RCA), Fishbone (Ishikawa) Diagrams, Failure Mode and Effects Analysis (FMEA), and the 5 Whys technique.
How is CAPA documented?
CAPA documentation involves detailed records of each phase, including identification of the problem, investigation findings, actions taken, verification results, and final approval. Proper documentation ensures traceability and regulatory compliance.
Who is responsible for CAPA in an organization?
CAPA responsibilities typically fall on the quality assurance team, but it involves cross-functional collaboration with departments like production, engineering, and regulatory affairs.
What are common pitfalls in CAPA processes?
Common pitfalls include inadequate root cause analysis, incomplete documentation, lack of timely action, and poor follow-up or verification. Ensuring thoroughness and compliance at each phase is essential.
How does CAPA relate to regulatory compliance?
Regulatory bodies like the FDA (Food and Drug Administration) require CAPA processes to be part of a quality management system (QMS) to ensure issues are systematically identified and addressed. Non-compliance can result in fines, recalls, or other penalties.
What are some best practices for effective CAPA?
Best practices include:
- Thoroughly documenting each phase.
- Conducting comprehensive root cause analyses.
- Implementing timely and effective corrective/preventive actions.
- Regularly reviewing and updating CAPA procedures.
- Training staff on CAPA processes and importance.
How is the effectiveness of CAPA actions verified?
Effectiveness is verified through monitoring outcomes, conducting follow-up audits, and evaluating whether the actions have successfully resolved the issue and prevented recurrence. Documentation of these activities is crucial for compliance and continuous improvement.