Why You Need A Quality System Manual
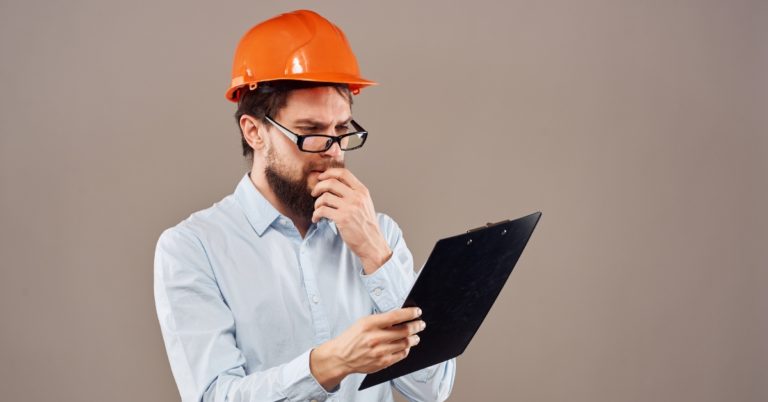
If you work in an industry that manufactures medicinal products, not strictly “medicines,” but any products used for medical purposes, you need a Quality System Manual.
Whether your products are as simple as an Ace bandage or as complex as an artificial heart valve, the Quality System Manual forms the basis for communicating how your organization intends to make an effective therapy that is marketed safely and legally.
In other words, the purpose of a quality manual is to document the quality objectives to produce safe, effective products, so all who read it have an understanding of (1) what the organization does, and (2) how the organization fulfills its objectives.
Safety
Medical devices and pharmaceuticals are a special set of products. These products have amazing potential to heal and to better human lives, but there is a downside to this potential, in that these products interfere with the human body to achieve their objectives. Such interference has the potential for harm, often severe harm.
Interference with the structure and function of the human body creates a need to eliminate (to the greatest extent possible) the potential for bodily harm caused by these products. It begins by creating organizational structures and work processes that sustain a system for consistently manufacturing error-free product. A Quality System Manual thereby saves human lives, and leads to saved liability costs and risks to the company manufacturing the medicinal products.
Domestic Requirement
Medical device manufacturers in the United States, should base their quality manual, minimally, on the requirements of 21 CFR 820, which is also called the “Quality System Regulation.” Important here is to outline what your company does, and specify which activities your company does NOT engage in. For example, if your company does not engage in installation and servicing activities or if your product is not sterile or not implantable, specifically state this in the quality manual to provide clarity.
Your company will save a great deal of backpedaling if an FDA inspector visits and finds that the quality manual specifies both included and excluded activities. If this information is missing, the inspector may get the impression that the organization performs undocumented activities, and this is a sure way to fail an inspection! Providing such specificity may seem tedious, but it is safer to over-communicate.
Aside from the audit benefits, getting specific helps staff to understand how their activities have the potential to adversely affect product quality (another FDA requirement). Be sure to provide justification for any excluded activities, as exclusion of an activity could be interpreted as a failure to institute a required activity.
International Expectation
The requirements of 820, the “Quality System Regulation,” closely mirror that of ISO 13485, which is an international standard for quality management for medical devices. Other international standards include the Medical Device Directive (MDD) which is currently enforced in Europe, and EU-MDR, the European Union Medical Device Regulation, which was expected for enforcement this May, but was postponed until next year, due to the pandemic.
If a company wishes to market a medical device, a quality management system, and its accompanying quality manual are required. Requirements are not a compelling reason for compliance. Business results are.
Business Results
A quality program is the best way to prevent the Cost of Poor Quality. Such costs cannot be quantified until poor quality reveals itself, so they are costs that are often overlooked at first. These costs are real, and include, warranty cost, product returns, rework expense, and product liability claims/lawsuits.
Further, and even more hidden costs include administrative costs processing deviations, managing through supplier contractual issues, processing complaints, manufacturing downtime, and sales lost from poor customer satisfaction. When companies proactively plan for avoiding these costs, as documented in the Quality System Manual, financial successes follow.
What About Pharma?
The pharmaceutical regulations, in 21 CFR 210/211, does not specifically require the Quality System Manual, but the concept still applies. An up-front plan for managing product safety and cost control yields evident business benefit.
Many pharmaceutical requirements have analogous requirements on the device side, for example, 21 CFR 211.22 requires that the responsibilities of the Quality Control Unit be in writing and followed (and has been the #1 most cited FDA-finding for pharma companies over 6+ years!). The Quality Manual is a tool for such written communication.
In fact, all the requirements for 21 CFR 210/211 can be framed within the context of a pharmaceutical quality management system, which can be documented in a pharmaceutical Quality System Manual. As a key communication tool, the Quality System Manual can ensure employees, customers, FDA inspectors, and the like understand, your organizational boundaries. Such boundaries help confine audit scope to the essential elements, potentially shortening the audit, with theoretically fewer audit findings.
Why Have A Quality System Manual?
The Quality System Manual establishes the what and why of the company and sets the tone for mutual understanding of the purpose of the organization and its commitment to quality.
It establishes how the company intends to produce safe and effective products and provides linkages to the Standard Operating Procedures (SOPs) that provide greater clarifying details about specific processes.
From a business perspective, the power of the Quality System Manual is the ability to provide a framework to prevent wasteful activities within a company, thereby improving a company’s bottom line.